Image
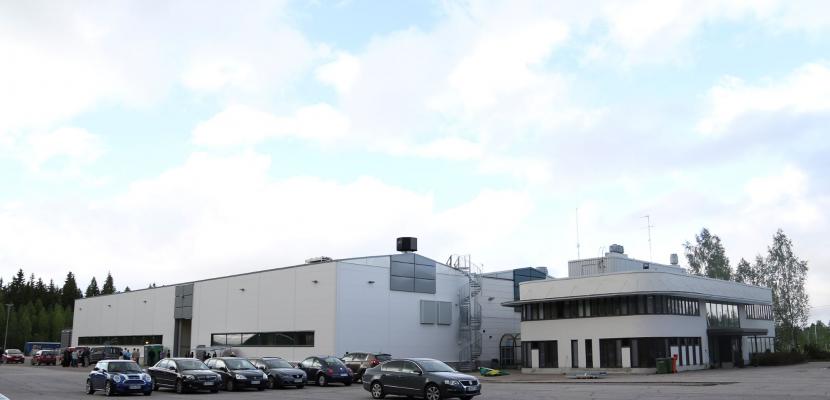
Geothermal heating and cooling of factory using heat pumps
Published on 05 November 2020

Finland
Etelä-Suomi
This is the good practice's implementation level. It can be national, regional or local.
About this good practice
Halton Marine wants to stand at the forefront of combating climate change and the company had a goal that all its operations around the world will be carbon neutral by 2025.
In Haltons marine HVAC systems factory in Lahti, heat pumps are used replaced the previous natural gas heating. Changing to heat pumps will save money as the price of natural gas keeps rising and also replace the aged cooling system at the same time.
The geothermal heat pump system consists of 22 heat wells, 310 to 330 meters deep, drilled into the land surrounding the plant. The ground stays at a steady temperature all year round allowing for heat to be captured in winter and transferred by the heat pump into the heating system of the factory.
During summertime, the same heat pumps are used for cooling. With the new heat pumps, the cooling capacity is increased enough that it can replace both the old process cooling and also cool the factory halls, thus improving working conditions.
In addition to the new system, Halton Lahti has invested in other energy-saving measures and signed a contract to only buy renewable electricity.
In Haltons marine HVAC systems factory in Lahti, heat pumps are used replaced the previous natural gas heating. Changing to heat pumps will save money as the price of natural gas keeps rising and also replace the aged cooling system at the same time.
The geothermal heat pump system consists of 22 heat wells, 310 to 330 meters deep, drilled into the land surrounding the plant. The ground stays at a steady temperature all year round allowing for heat to be captured in winter and transferred by the heat pump into the heating system of the factory.
During summertime, the same heat pumps are used for cooling. With the new heat pumps, the cooling capacity is increased enough that it can replace both the old process cooling and also cool the factory halls, thus improving working conditions.
In addition to the new system, Halton Lahti has invested in other energy-saving measures and signed a contract to only buy renewable electricity.
Resources needed
System is delivered by external turnkey solutions provider and requires no extra workforce for the company. System was paid directly by the company with no loans involved. Cost 607 000 € of which 15% subsidized by energy aid grant. Payback period of 8 - 10 years. Land is also needed for wells.
Evidence of success
1.8 – 2.5 M€ Lifetime savings estimated for the system by saving money on gas, with annual saving of around 60 000 €.
90% reduction in emissions from heating adding to 103 tons/CO2 per year.
35 % savings on heating energy costs annually.
Money was saved on buying a new separate cooling system as the old cooling system was also reaching the end of its lifespan. Added cooling of work spaces improves productivity in summer.
90% reduction in emissions from heating adding to 103 tons/CO2 per year.
35 % savings on heating energy costs annually.
Money was saved on buying a new separate cooling system as the old cooling system was also reaching the end of its lifespan. Added cooling of work spaces improves productivity in summer.
Potential for learning or transfer
Heat pumps are a good option for any country with low electricity prices and the need for heating. However, they are not profitable if electricity is too expensive.
Further information
Website
Good practice owner
You can contact the good practice owner below for more detailed information.
Organisation
Lab university of applied sciences

Finland
Pohjois- ja Itä-Suomi
Contact
RDI specialist