Image
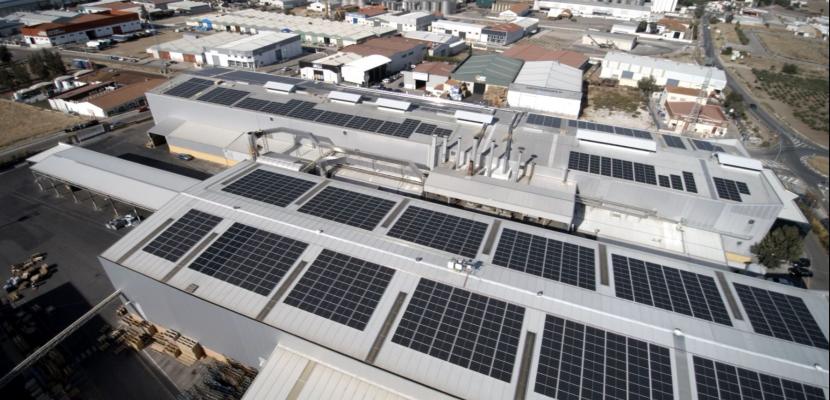
Roof-top photovoltaic plant ALUMASA
Published on 14 December 2020

Spain
Extremadura
This is the good practice's implementation level. It can be national, regional or local.
About this good practice
ALUMASA (Aluminios del Maestre S.A) was founded in 2000 to produce lacquered aluminium rolls with a production rate of 14.000 t per year.
The current electricity energy consumption that the factory has is 9 GWh.
Due to these reasons, ALUMASA decided to install a rooftop PV plant, however, the initial investment needed was too high, the company decided to split the process into two phases.
The factory used 2 industrial warehouses with a surface occupancy of 9.285 m2 and 21.535 m2.
Phase 1 (March-July 2020)
- The company installed at the roof of the factory 3240 PV modules producing 425 Wp each one. This achieves 1,36 MWp of the total power produced.
- The rooftop surface used was situated at one of the main industrial warehouses, taking up 8.000 m2.
- The installation counts with 11 inverters which function is to convert the direct current (DC) output of the PV panel into alternating current (AC). To be used for self-consumption in the factory.
- At this phase, the factory reduced the CO2 emissions by 782 t per year.
- The saving of energy that the factory had at this phase was 16%.
Phase 2 (Will start on December 2020 )
- With this future intervention, the factory wants to add to the first phase 1,6 MWp, making a total amount of 2,96 MWp.
- The rooftop surface used will be 9.412 m2.
- With savings of 19% of energy.
- The avoided emissions will be 920 t per year.
The current electricity energy consumption that the factory has is 9 GWh.
Due to these reasons, ALUMASA decided to install a rooftop PV plant, however, the initial investment needed was too high, the company decided to split the process into two phases.
The factory used 2 industrial warehouses with a surface occupancy of 9.285 m2 and 21.535 m2.
Phase 1 (March-July 2020)
- The company installed at the roof of the factory 3240 PV modules producing 425 Wp each one. This achieves 1,36 MWp of the total power produced.
- The rooftop surface used was situated at one of the main industrial warehouses, taking up 8.000 m2.
- The installation counts with 11 inverters which function is to convert the direct current (DC) output of the PV panel into alternating current (AC). To be used for self-consumption in the factory.
- At this phase, the factory reduced the CO2 emissions by 782 t per year.
- The saving of energy that the factory had at this phase was 16%.
Phase 2 (Will start on December 2020 )
- With this future intervention, the factory wants to add to the first phase 1,6 MWp, making a total amount of 2,96 MWp.
- The rooftop surface used will be 9.412 m2.
- With savings of 19% of energy.
- The avoided emissions will be 920 t per year.
Resources needed
The fundings used to develop both phases of the installation were private.
The total invest of both installations has been 1.814.046 € (PH1+PH2)
with an investment cost per install kW of 599 €/kW.
The total invest of both installations has been 1.814.046 € (PH1+PH2)
with an investment cost per install kW of 599 €/kW.
Evidence of success
As a consequence of the installation date when it was completed. They have not achieved any results yet. However, the studies made by the engineers are successful, suggesting a 35 % savings in the energy consumption of the factory.
Potential for learning or transfer
This factory is one of the most successful factories in the region, generating 160 employments, and producing 20.000 t per year. These numbers had encouraged the company to get RES installations onboard.
The first step was to hire engineers to study factory consumption and to know how RES could improve energy consumption at the factory.
Emececuadrado made an initial study suggesting ALUMASA split the installation into 2 phases, in order to have an easier adaptation period for the PV installation.
The two main lessons this enterprise can transfer are:
- The study was carried out by the engineers from Emececuadrado with regards to the viability of the installation.
- The way the company has achieved the intervention by splitting into two phases.
The first step was to hire engineers to study factory consumption and to know how RES could improve energy consumption at the factory.
Emececuadrado made an initial study suggesting ALUMASA split the installation into 2 phases, in order to have an easier adaptation period for the PV installation.
The two main lessons this enterprise can transfer are:
- The study was carried out by the engineers from Emececuadrado with regards to the viability of the installation.
- The way the company has achieved the intervention by splitting into two phases.
Further information
Website
Good practice owner
You can contact the good practice owner below for more detailed information.
Organisation
ALUMASA (Aluminios del Maestre S.A)

Spain
Extremadura
Contact
PROJECT MANAGER