Image
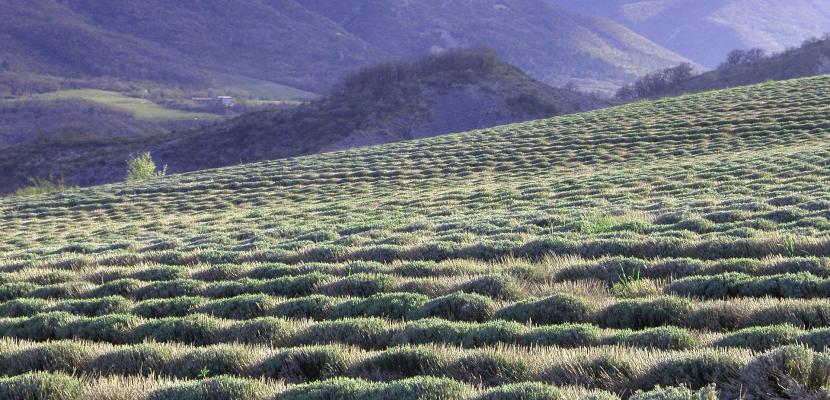
Dryficiency: Use of Waste Heat for Starch Drying
Published on 23 March 2021

Austria
Steiermark
This is the good practice's implementation level. It can be national, regional or local.
About this good practice
The overall objective of DryFiciency project is to lead the European energy intensive industry to high energy efficiency and a reduction of fossil carbon emissions by means of waste heat recovery. Turning waste heat into renewable energy – recycling heat – is a difficult process to achieve, which is mainly result of a non-standardized set of definitions which would link renewability and diverse waste heat source, as well as due to the lack of technologies that make the process feasible. However, the process significantly impacts greater savings and energy efficiency - as half of the energy produced is wasted and of which the majority of is in the form of heat. The project targets this challenge through pilot projects aimed at the installation and the use of compression heat pumps (CHP) for industrial drying processes. The new technology is intended to recover the energy content of the water vapor from the exhaust air and transfer it back into the drying process.
DryFiciency´s vision is to foster competitiveness, improve security of energy supply and promote sustainable production in Europe by mainly focusing on the application of heat pump in industrial drying and dehydration processes of the agricultural, ceramic, and pet feed industry.
DryFiciency´s vision is to foster competitiveness, improve security of energy supply and promote sustainable production in Europe by mainly focusing on the application of heat pump in industrial drying and dehydration processes of the agricultural, ceramic, and pet feed industry.
Resources needed
The DryFicieny project is funded by Horizont Europe 2020 program, under the program priority "Valorisation of waste heat in industrial systems (SPIRE PPP)", with the total amount of 1.5 mil EUR.
Evidence of success
The potential of the technology demonstrated within the Dryficiency’s consortium is to reduce the specific energy demand for drying and dehydration from 700-800 kWh per ton down to 200 kWh per ton of evaporated water. The energy switch from fossil fuels towards heat pump technology reduces the environmental impact considerably and offers at the same time a potential for energy savings of up to 60-80%.
Potential for learning or transfer
In the scope of the project, heat-pump technology is used to dry bricks, which is traditionally dried with hot air in “open” convection driers. Innovation which applies to the process provides new ways to run it in a closed circuit - with the heat pump recovering heat from the moist exhaust air and returning it to the heating system. This provides wide areas of opportunities in application of such methods and further improvement in production processes of various industries, especially in terms of sustainability and energy efficiency. While many governments offer subsidies and tax breaks for renewable energy sources such as solar and wind power, the subsidies provided for waste heat recovery are quite small in comparison. To allow greater use of waste heat as a renewable energy source in industrial processes, regions need to balance treatment of the different waste heat sources and this way improve accessibility of resources.
Good practice owner
You can contact the good practice owner below for more detailed information.
Organisation
Vorarlberg University of Applied Sciences

Austria
Vorarlberg
Contact
Scientific research