Image
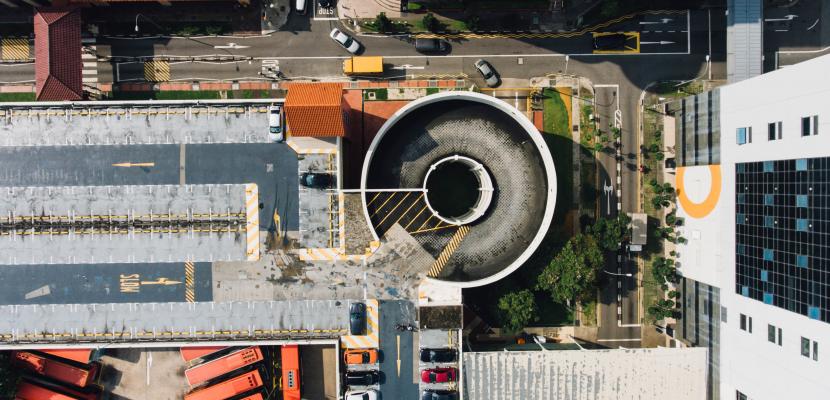
Renewable Steel Gasses: Integration of renewable energy in steel production
Published on 23 March 2021

Austria
Niederösterreich
This is the good practice's implementation level. It can be national, regional or local.
About this good practice
The integration of renewable energy with subsequent methanation in a steel plant anticipates a significant increase of energy efficiency in the steel production, a substantial reduction of greenhouse gas emissions as well as chemical storage of renewable excess energy which can be utilized externally and within the steel plant, respectively. The synergetic use of by-products of PtG within the steel plant, particularly oxygen, promises further energetic efficiency increase as well as costs savings which improve the profitableness of the process chain to be developed.
As result of this project, one or more optimal integration variants of PtG and biomass gasification with an integrated steel plant should be developed, the increase of energy efficiency of steel production compared with the state-of-the-art (BAT) and the CO2 reduction potential should be quantified, and a basic engineering of such process chain for subsequent implementation in demonstration scale should be worked out. The aim of voestalpine is to reduce CO2 emissions by initially converting a part of our carbon-based steel production using the integrated blast furnace route into electric steel production, flexibly combining raw mate-rials and increasing the use of hydrogen (natural gas, coke gas or pure hydrogen) and renewable energy.
As result of this project, one or more optimal integration variants of PtG and biomass gasification with an integrated steel plant should be developed, the increase of energy efficiency of steel production compared with the state-of-the-art (BAT) and the CO2 reduction potential should be quantified, and a basic engineering of such process chain for subsequent implementation in demonstration scale should be worked out. The aim of voestalpine is to reduce CO2 emissions by initially converting a part of our carbon-based steel production using the integrated blast furnace route into electric steel production, flexibly combining raw mate-rials and increasing the use of hydrogen (natural gas, coke gas or pure hydrogen) and renewable energy.
Resources needed
The project is supported with financial contribution from the Austrian "Climate and Energy Fund" as a part of the research program "Energieforschung", accounting the total cost of project implementation for about 720.000 EUR.
Evidence of success
Main result of the project is the development of an optimal integration variants of PtG and biomass gasification with an integrated steel plant, alongside to the quantification of the amounts of the increase in energy efficiency of steel production compared with the state-of-the-art and CO2 reduction potentials. In addition, project output propose a basic engineering of such process chain for subsequent implementation in demonstration scale.
Potential for learning or transfer
Solutions offered by the project could be advanced by the experimentation on a larger system scale, requiring techno-economic improvements. Still, since electricity cost is the main cost driver and since it is expected that the electricity will be even more expensive in the future, improvements in system efficiency could be impacted by its techno economic feasibility. This implies that further policy improvements could target further technologies uptake and its potential effects on improving electrolyser and biomass gasification. In addition, efficiency of the implemented process could be improved by changes in existing regulations targeting specifically emission trading.
Good practice owner
You can contact the good practice owner below for more detailed information.
Organisation
Vorarlberg University of Applied Sciences

Austria
Vorarlberg
Contact
Scientific research