Image
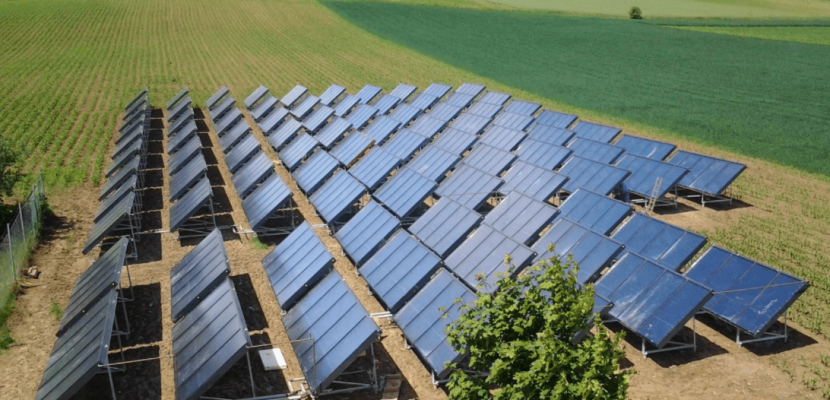
Flat-Plate Solar Collectors at Fleischwaren Berger for Boiler Feed-water Preheating
Published on 03 December 2020

Austria
This is the good practice's implementation level. It can be national, regional or local.
About this good practice
Fleischwaren Berger is an Austrian family business which grew into a company with 500 employees and sales volume of 125 mils. € p.a. (2012). 80-100 tons of meat are delivered to the company Berger daily and are mainly produced to ham and sausage-products. The company uses ca 10 GWh electricity each year for the production, 50 % of that for the cooling system, and additionally 14 GWh fuel oil for the company´s thermal energy demand. Thus, the company spends around 2 million € for energy per year.
The company decided to build a solar process heat plant to save recources. The plant was designed and installed by SOLID and taken into operation in the of July 2013. The collector field with 1.067m2 of area was installed on an open field next to the production site.
The gross flat plate collectors are equipped with a second cover made of a heat resistant foil beneath the glass cover. The collector field has a maximum performance of around 0,6 MWth. Specific collector earnings are of 465 kWh/m² per year. Solar heat price results in 27 €/MWh including funding (an interest rate of 2.5 % was applied to the calculation).
The heat produced by the collector field is stored in a 60 m3 buffer tank which is designed for a pressure of 4 bar and heated up to a temperature of up to 110 ˚C. The hot water is then used for preheating of boiler feedwater and for cleaning purpoces of the process technology.
Total project costs: 790 000 EUR
The company decided to build a solar process heat plant to save recources. The plant was designed and installed by SOLID and taken into operation in the of July 2013. The collector field with 1.067m2 of area was installed on an open field next to the production site.
The gross flat plate collectors are equipped with a second cover made of a heat resistant foil beneath the glass cover. The collector field has a maximum performance of around 0,6 MWth. Specific collector earnings are of 465 kWh/m² per year. Solar heat price results in 27 €/MWh including funding (an interest rate of 2.5 % was applied to the calculation).
The heat produced by the collector field is stored in a 60 m3 buffer tank which is designed for a pressure of 4 bar and heated up to a temperature of up to 110 ˚C. The hot water is then used for preheating of boiler feedwater and for cleaning purpoces of the process technology.
Total project costs: 790 000 EUR
Expert opinion
Co-funded by FP7 (50%), the Austrian Research Promotion Agency (15%) and the private sector, this project is a good practice application of solar thermal energy for industrial applications. Unlike for domestic hot water use, solar thermal can supply mid-temperature process heat to commercial operations. This area is still under-used and this project demonstrates its feasibility and suitability.
Lack of familiarity with this type of applications and lack of scale make public co-funding for such projects a prerequisite.
Lack of familiarity with this type of applications and lack of scale make public co-funding for such projects a prerequisite.
Works at
Interreg Europe Policy Learning Platform
Resources needed
Energy audit, human resources to design and install the solar thermal collectors, financial resources. Total project costs: 790 000 EUR, with a 15% subsidy of Austrian Research Promotion Agency (ARPA) and 50% subsidy from the InSun project.
Evidence of success
Thanks to the solar process heat plant, the company Fleischwaren Berger saves 62.500 l of fuel oil a year and preserves the environment by greenhouse gas emissions of 163 tons – a saving of 4 – 5 % on the company’s total fuel oil consumption.
Potential for learning or transfer
This practice from meat processing industry provides a great overview of how solar thermal collectors may reduce the heat demand which had previously been covered by fossil fuels and replacing the heat for renewable energy source. As the boiler make-up water is preheated by the system and then fed into a buffer to be used within the site for cleaning or rinsing or as a feed water for the steam boiler, which both of these are very common uses of hot water and not only specific for the meat processing industry, this practice illustrates a potential application of solar thermal for a broad spectrum of process industry.
Further information
Website
Good practice owner
You can contact the good practice owner below for more detailed information.
Organisation
Fleischwaren Berger GmbH&Co

Austria
Niederösterreich
Contact
Energy engineer in R&D