Image
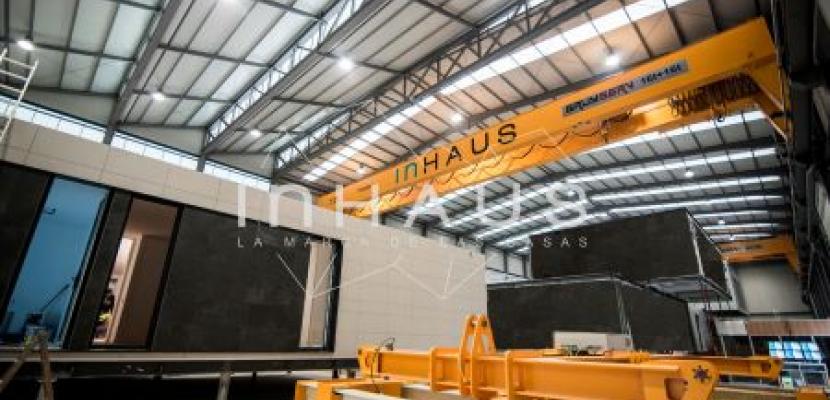
Industrialized, reassembling and reusable buildings that REDUCE environmental impact.
Published on 26 June 2020

Spain
Comunitat Valenciana
This is the good practice's implementation level. It can be national, regional or local.
About this good practice
Industrialization and modularization are key aspects that contribute to CE and buildings life-extension. This practice promotes prefabrication and modular systems. The company offers a catalogue of houses (combination of modulated spaces), with several finish style available. The industrialized construction allows the reduction of waste to a minimum, as well as a controlled and efficient management of it. Dry construction reduces water consumption, allows the later disassembly of the modules or materials used in case of a building re-location or at the end of its life cycle. 82% of materials can be recovered and reused later. But also, recyclable materials are used (% depend on the style finish chosen).
Regarding environmental impact, all subcontractors and employees are locally based, so displacement and associated emissions are reduced. Onsite settle time is very reduced (2-3 days), so there are no long periods to bother neighbourhood (noises, dust production, roads occupation/obstruction by machinery, etc).
The company has agreements with various public administrations (chamber of commerce, municipalities) for employee training in its industrialized systems. Programs are especially aimed at unemployed people: youngster, women and those over 50 years.
Banks facilitate access to financing for the self-promotion of the house because they perceive less risk as the delivery date and budget are closed in advance, and there are not unforeseen expenses.
Regarding environmental impact, all subcontractors and employees are locally based, so displacement and associated emissions are reduced. Onsite settle time is very reduced (2-3 days), so there are no long periods to bother neighbourhood (noises, dust production, roads occupation/obstruction by machinery, etc).
The company has agreements with various public administrations (chamber of commerce, municipalities) for employee training in its industrialized systems. Programs are especially aimed at unemployed people: youngster, women and those over 50 years.
Banks facilitate access to financing for the self-promotion of the house because they perceive less risk as the delivery date and budget are closed in advance, and there are not unforeseen expenses.
Resources needed
82 people to build a house 300m2 in 8 weeks
Evidence of success
The company started its activity 8 years ago. At the beginning the staff was composed by 5 architects and now there are 82 people working directly in the factory, and 60 people are subcontracted.
The system is being transferred now to the tourism sector (hotels) which have seen an added value in the possibility to move the buildings to another location, in case the initial one is not profitable enough, other destination become popular, or in anticipation of the possible impact of climate change
The system is being transferred now to the tourism sector (hotels) which have seen an added value in the possibility to move the buildings to another location, in case the initial one is not profitable enough, other destination become popular, or in anticipation of the possible impact of climate change
Potential for learning or transfer
Traditionally the construction sector in Spain and Valencia region has been a low-industrialised and highly labour-intensive sector, which means lower quality, less precision, higher risk of unforeseen events and economic deviations, much generation of surpluses, greater environmental impact. Industrialised construction improves all above aspects. In addition, this practice improves working conditions of employees, and has a positive impact on the environment by less resource’s consumption.
Public administrations can benefit from the costs savings and increased productivity linked to modular and prefabricated construction since this approach fits perfectly with some of building typologies (e.g. schools) promoted by public entities, with repeatable, and easily standardizable, spaces and elements. The public sector has an important role for the adoption of these practices, by including offsite manufacturing targets in public tenders, but also by modernizing building codes & regulations
Public administrations can benefit from the costs savings and increased productivity linked to modular and prefabricated construction since this approach fits perfectly with some of building typologies (e.g. schools) promoted by public entities, with repeatable, and easily standardizable, spaces and elements. The public sector has an important role for the adoption of these practices, by including offsite manufacturing targets in public tenders, but also by modernizing building codes & regulations
Further information
Website
Good practice owner
You can contact the good practice owner below for more detailed information.
Organisation
Casas inHAUS S.L

Spain
Comunitat Valenciana
Contact
Project Manager