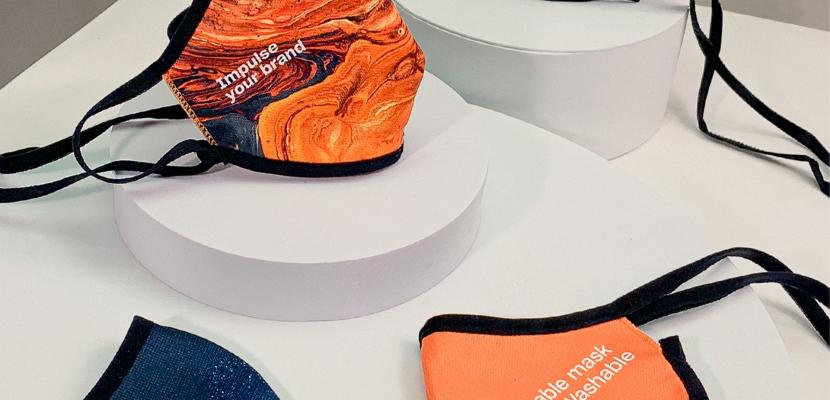
Upcycling for resilience: Sustainable face masks

About this good practice
At the beginning of the COVID-19 crises there was a shortage in the supply of face masks, mainly due to a surge in demand.
Surgical masks and other common face masks are disposable, creating high environmental impacts such as resource’s consumption, waste generation and littering or microplastic and microfiber generation due to their disintegration.
One of the challenges posed by the pandemic was thus the need for more sustainable face masks.
In this context, ARPE, a small textile company located in the province of Barcelona, started the design and manufacturing of a sustainable customizable face mask model.
The masks have the following features:
• local manufacturing: manufactured in ARPE’s plant situated in the province Barcelona, using 100% renewable energy;
• from post-consumer r-PET;
• 99% less CO2 than a FFP2 mask;
• tested up to 50 washes.
Companies, retailers, public authorities, universities, among others, are the main potential beneficiaries of this initiative since ARPE’s masks are customizable.
Resources needed
During the first months of the pandemic, all the company’s human resources (22 internal workers + external collaborators) and all its equipment focused on the manufacturing of new masks/fabrics needed for masks.
Evidence of success
The project was a huge success and is, in fact, still ongoing, even though the sales have now dropped considerably.
The mask obtained the CONAMA (Spanish Congress for the Environment) Ecodesign Award 2020 and the PIMEC (Association of SMEs) Award for the adaptive capacity to the pandemic. Plus, they were also PSI Sustainable Product Winner 2021.
Potential for learning or transfer
Key success factors:
• Leadership
• High level of motivation: “never give up”
• To align all the team members towards the same objective
• Having a committed team, which is related both to motivation and alignment
• Having a creative team that was able to find a solution for every challenge
• Having the production process vertically integrated was an advantage because it allowed ARPE to develop prototypes and undertake tests internally (which implied not having to depend on other companies)
• “A little bit of luck”
Although all these elements were mentioned as important by ARPE, they consider that the most important success factor was having a committed and creative team.
Further information
Good practice owner
You can contact the good practice owner below for more detailed information.