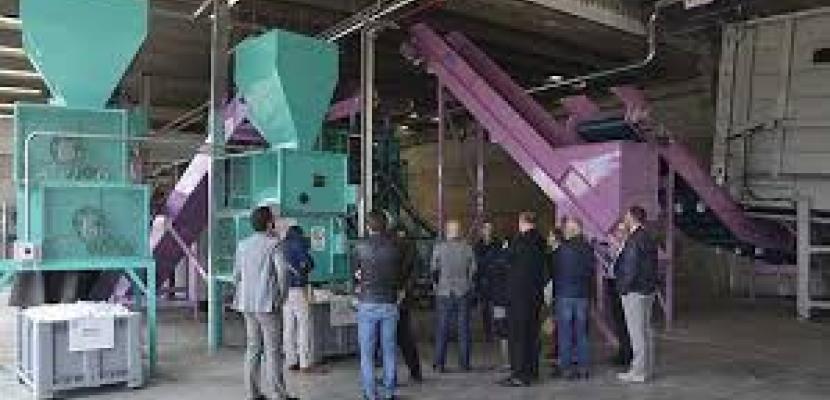
Fater SMART - Diaper Recycling

About this good practice
AHPs waste contribute between 2-4% of the total Municipal Solid Waste. Each year 900,000 tons of AHP waste are incinerated or landfilled in Italy, 8,500,000 tons in Europe and over 30,000,000 tons in the world.
FATER provides AHP separated collection and an autoclave treatment process where AHP are sanitized, de-composed and dried, leading to the recovery of its valuable components (mostly high-quality cellulose and specialty plastics). The recycled diapers become urban furniture and many other items of daily use such as cardboard for industrial packaging and fertilizers thus giving a new life to that which just a few years ago was considered a non-recyclable waste product.
This industrial eco-system starts in 2012 with the project “RECALL - REcycling of Complex AHP waste through a first time application of patented treatment process and demonstration of sustainable business model” co-funded by the European Commission under the CIP Eco-Innovation - Pilot and Market Replication Projects Call 2011. Partners participated: CONTARINA SPA; FATER SPA; AMBIENTE ITALIA SRL; COMUNE DI PONTE NELLE ALPI; EUROPEAN PLASTICS RECYCLERS from Belgium.
Expert opinion
Diaper recycling is an innovative approach to managing the waste generated by disposable diapers, which can take hundreds of years to decompose in landfills. Traditional disposable diapers are made from a combination of materials, including plastic, absorbent polymers, and organic materials, making them challenging to recycle. While this good practice represents an innovative step forward in the diaper recycling space, widespread adoption and scalability are still in development stages. Some of the challenges include separate collection methods and a legislation framework which permitsto the sale of end products of the recycling proces. In any case, this initiative is in line with the EU Circular Economy Action Plan and a widespread adoption of this solution would contribute to meeting the overall recycling target of 65% by 2035.
Resources needed
Actually the plant employs 15 employees working for future development of the technology.
Evidence of success
- Recycling allows the recovery of high-quality secondary raw material with a number of new uses. 150 kg (330 lbs.) of cellulose, 75 kg (165 lbs.) of plastic, and 75 kg (165 lbs.) of superabsorbent polymer may be recovered upon recycling of each metric ton of such waste.
- The emissions avoided are by far greater than those generated by the recycling system as a whole.
- Jobs opportunities increased:15 new employees.
Potential for learning or transfer
To set up the FaterSMART technology means accessing new markets and a new business, thanks to the increase in revenue from the disposal of used absorbent hygiene products and to the new revenue from sales of secondary raw material of a higher quality level than the corresponding standard recycled materials.
The FaterSMART -branded innovation takes on particular relevance especially in contexts where it is possible to reach or exceed the recycling targets established by legislation. In fact, in contexts where over 70-80% of waste is recycled, used absorbent hygiene products account for up to 20-25% of non-recycled residual waste.
Further information
Website
Good practice owner
You can contact the good practice owner below for more detailed information.
FATER S.PA.
